Forward thinking from Kverneland Group in Italy
Manufacturers are always keen to impress upon us the quality and the value of their products to the end user, yet, of equal importance to customers, is the ethos and integrity of the company they are dealing with.
The Kverneland Group is one company that has been increasingly active over the past year in developing its range and putting itself forward as the company to do business with, and, as part of this drive they recently invited the European press to their Italian facilities.
Seeing is believing
The acquisition of ROC was obviously at the top of the agenda, but there was a good deal more news centred around the existing Kverneland range of machinery.
Much of what was new centred around the incremental development of machines with no great breakthroughs or innovations being announced, yet field demonstrations can give an excellent indication of how companies are approaching the future.
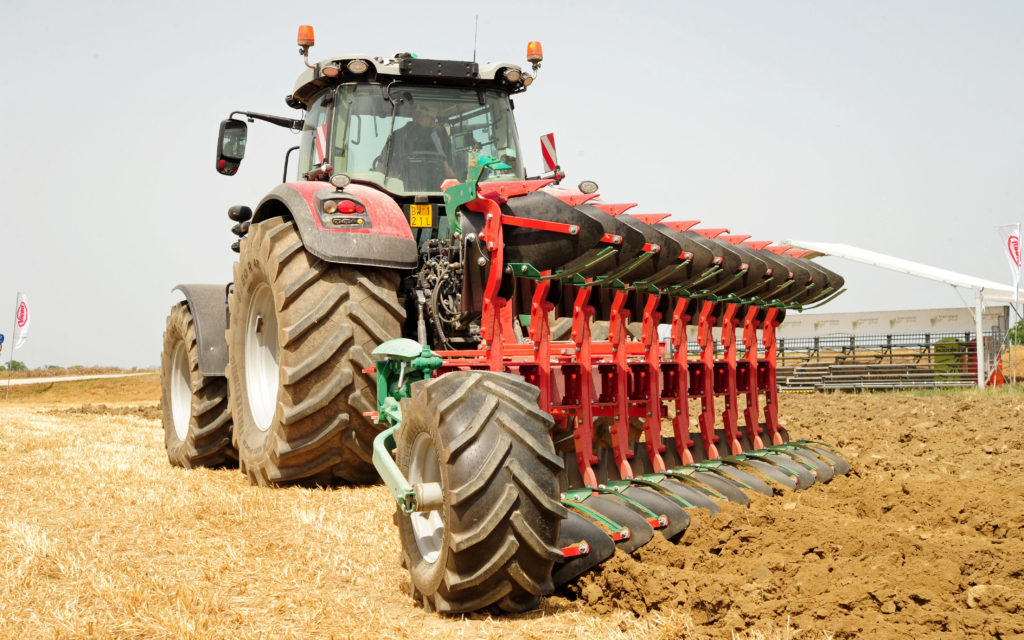
Kverneland is known for its ploughs; it claims to have around 70% of the Irish market, a share which has been built on the products’ robustness and performance.
Yet the plough is under pressure; the green lobby believe it to be the antithesis of ecological farming and there is much muttering of its detrimental effect on carbon sequestration.
This has not deterred Kverneland, which has gone on to produce a plough that meets many of the criticisms half way.
Shallow working depth
The Ecomat On-Land plough is designed to work at the shallower depth of just 6in. This obviously reduces the draught requirement and so, fuel consumption.
Burial of trash is aided by deflectors mounted parallel to the top of the plough body, which direct the upper surface of the soil downwards as it moves to the top of the body, thus ensuring a more complete burial.
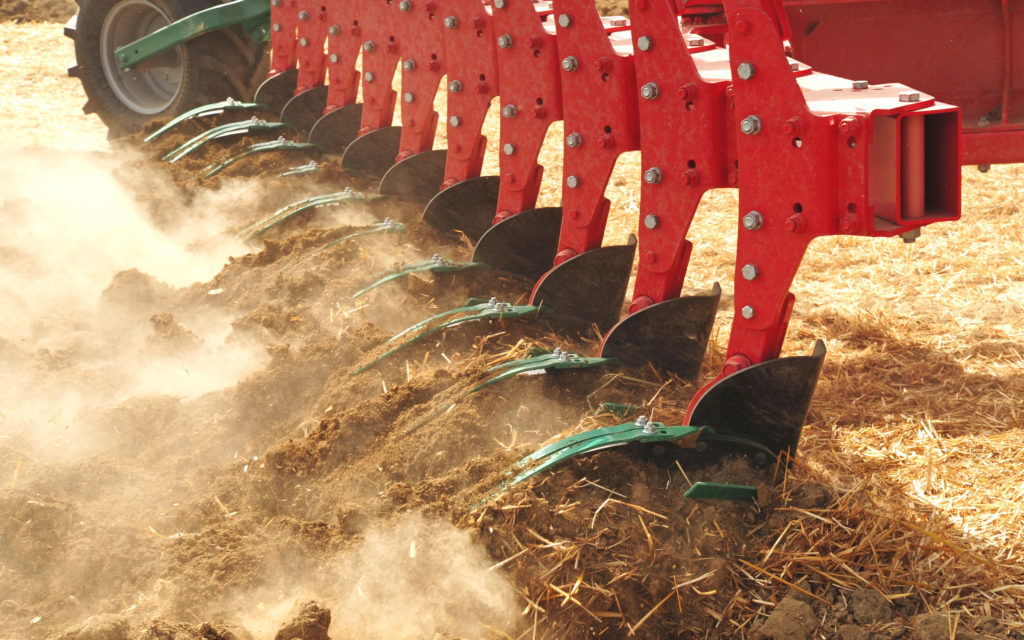
The plough is pulled by the tractor running on the land instead of in the furrow, this allows low ground pressure tyres to be used, reducing overall soil compaction.
The company has adapted an ancient and well-proven implement to modern requirements, underlining the fact that simply abandoning a tool because it doesn’t meet the perceived demands of the day is a short-sighted policy.
Baler strategy
The Kverneland Group has taken a thoughtful approach to product development. This can also be seen how it is progressing in the design of round balers, and here they are moving forward with a determination that speaks of long-term objectives.
There are two major routes being taken: The first is by the continued development of the Fastbale non-stop baler, while the second is by the integration of Tractor Implement Management (TIM) into the baler range.
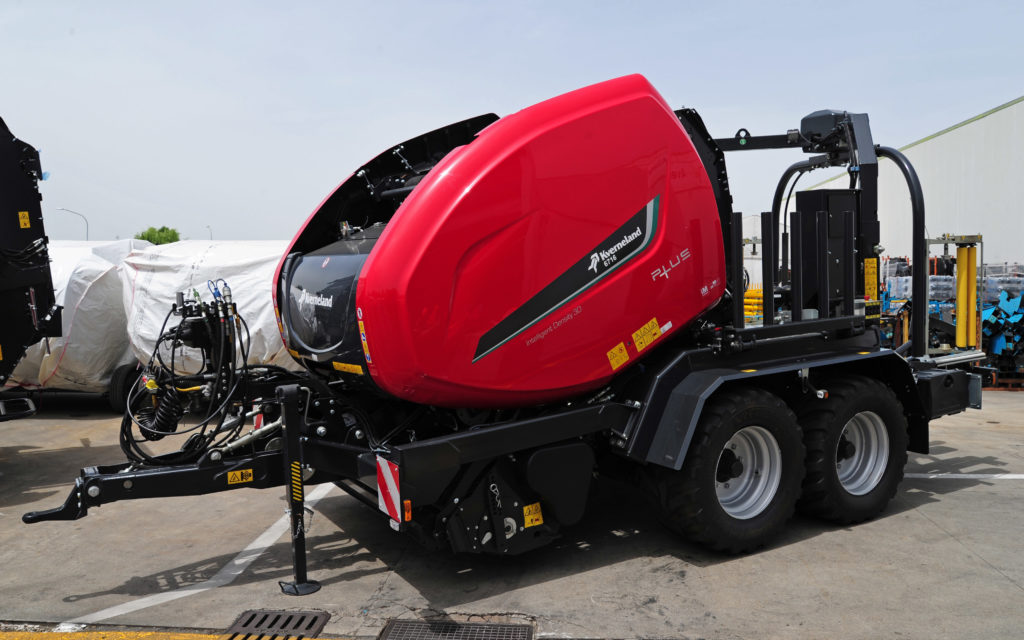
The Fastbale continuous baler got off to a shaky start when it was first introduced to Ireland, and elsewhere. But Kverneland has stuck with it and brought it on to a machine that can be regarded as reliable as any other baler they produce.
Obviously, the great advantage is that there is no need to stop the tractor to eject the bale, which is said to give a 30% increase in productivity.
In addition to the improved work rate there is less stress on both the tractor and driver.
There are a growing number being operated in Ireland and Philip English, CEO of Kverneland in Ireland, is optimistic about further sales, believing they have now reached market acceptance.
Digital aids to operation
Continuous baling was not being demonstrated on the day, yet the other move forward was, in the shape of the the TIM-enabled RV5216 (Vicon designation) baler.
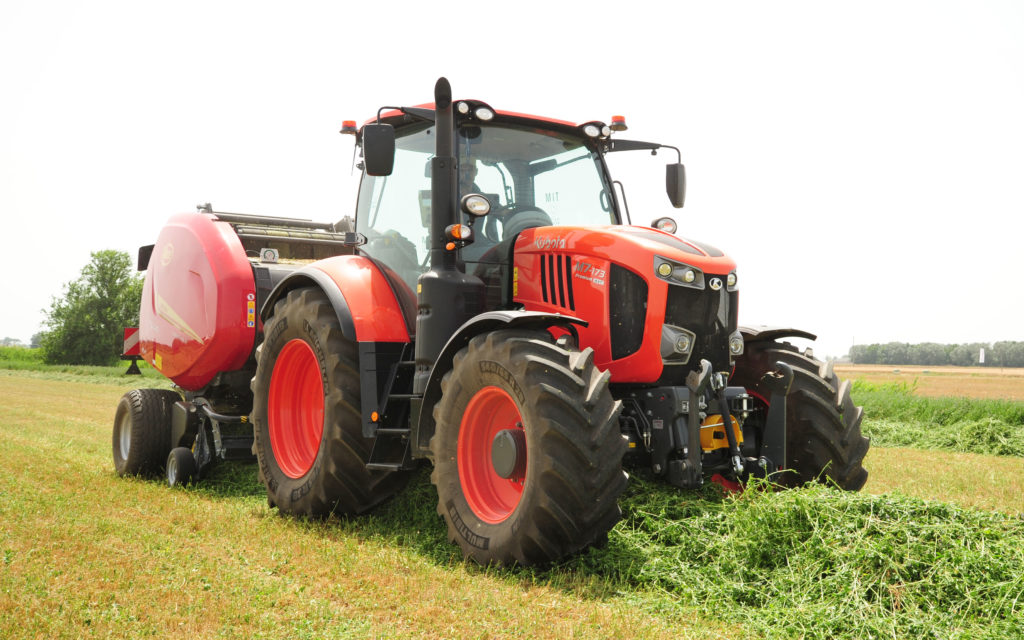
Kubota has long considered digital technology as being primarily an aid to the operator rather just a tool for collecting and shuffling data around the block, and with TIM this becomes a reality.
With the baler taking over many tasks of the operator in controlling the tractorm baling is said to be less tiring and more efficient – it is also likely to reduce stress on the machinery itself.
Unfortunately, it was not possible to sit in the cab and watch the system work, but we were assured that the baler was doing much of the work of the operator, including stopping the tractor for bale ejection.
Taking the baler to the next level
Taking these two factors into consideration, it is clear that the company is forging ahead in baling technology and it will be for other manufacturers to keep up.
It is not just in the field that advances are being made. The baler assembly process has undergone a thorough review by Kubota to increase quality, efficiency and output.
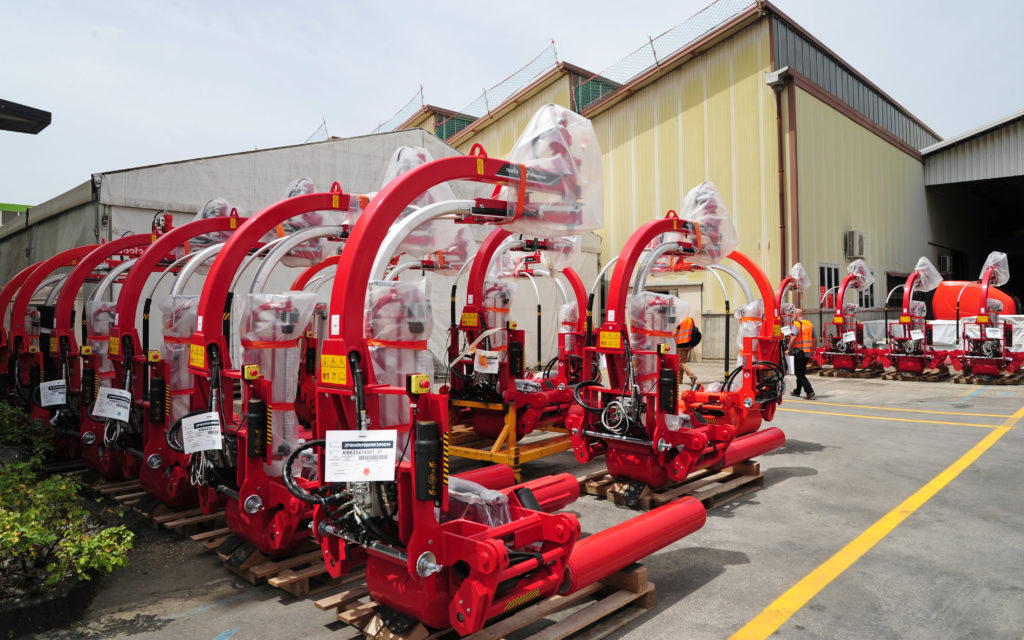
The assembly plant at Ravenna, an hour’s drive north of the newly acquired ROC factory, now has the capability to produce 12 balers/day as opposed to the eight prior to its upgrade.
Much of this is due to automation, with the frames now being welded by robots which leaves a neat and predictable joint, indeed, the bare chassis before assembly gives every impression of rigidity and strength.
Once complete, the balers are fully tested prior to being stored under a cover before dispatch, ensuring they arrive at dealerships in the best possible condition.
Company outlook
Kubota purchased the Kverneland Group in late 2011 as Japanese companies looked to manufacture abroad due to the strong yen making exports expensive.
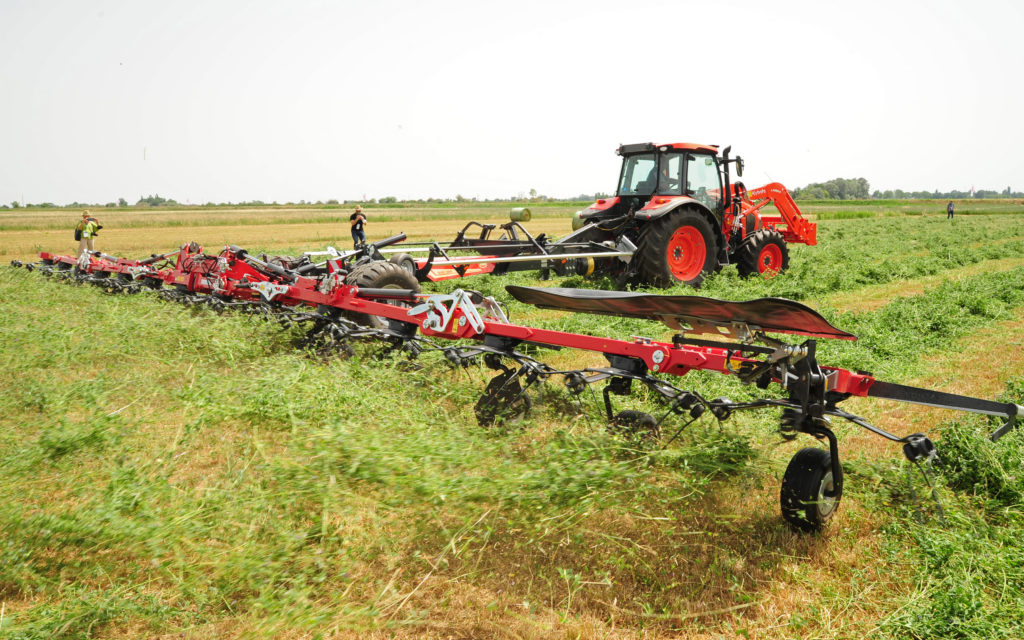
It was said at the time that Claas and Same Deutz Fahr were also in its sights but, so far, they remain as independent companies.
Just one year before, the Kverneland Group had invested in the Italian baler manufacturer Gallignani, and it is this factory which lies at the heart of its baler production operation at Ravenna.
Where next for the Kverneland Group?
Worldwide sales for Kverneland implements now amount to €20 billion annually and that figure is only set to grow with the purchase of ROC.
Naturally, the company is shy about plans for any further acquisitions, preferring, instead, to focus on plans for organic growth, noting that there will be a strong demand for machinery for a long time to come.
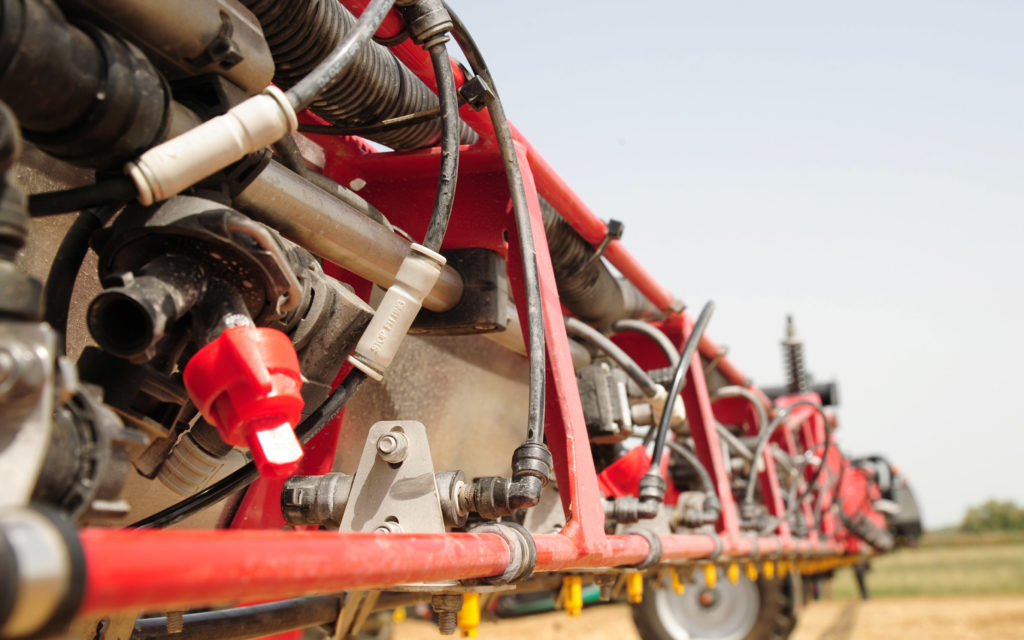
It also chose to highlight its digital vision with machine actuation at the top of the chain, rather than data collection and management.
However, the great digital matrix known as Agricultural 4.0 was also mentioned as being relevant to growth, yet when asked if such a grandiose scheme would be vulnerable to hacking of the type experienced by AGCO, there came only the reassurance that security is constantly under review.